Liquid Penetrant Testing (PT)
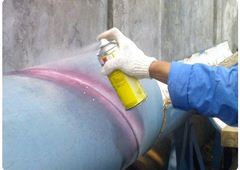
The basic principle of liquid penetrant testing is that when a very low viscosity (highly fluid) liquid (the penetrant) is applied to the surface of a part, it will penetrate into fissures and voids open to the surface. Once the excess penetrant is removed, the penetrant trapped in those voids will flow back out, creating an indication. Penetrant testing can be performed on magnetic and non-magnetic materials, but does not work well on porous materials. Penetrants may be "visible", meaning they can be seen in ambient light, or fluorescent, requiring the use of a "black" light. The visible dye penetrant process is shown in Figure 7. When performing a PT inspection, it is imperative that the surface being tested is clean and free of any foreign materials or liquids that might block the penetrant from entering voids or fissures open to the surface of the part. After applying the penetrant, it is permitted to sit on the surface for a specified period of time (the "penetrant dwell time"), then the part is carefully cleaned to remove excess penetrant from the surface. When removing the penetrant, the operator must be careful not to remove any penetrant that has flowed into voids. A light coating of developer is then be applied to the surface and given time ("developer dwell time") to allow the penetrant from any voids or fissures to seep up into the developer, creating a visible indication. Following the prescribed developer dwell time, the part is inspected visually, with the aid of a black light for fluorescent penetrants. Most developers are fine-grained, white talcum-like powders that provide a color contrast to the penetrant being used.
PT Techniques
Solvent Removable
Solvent Removable penetrants are those penetrants that require a solvent other than water to remove the excess penetrant. These penetrants are usually visible in nature, commonly dyed a bright red color that will contrast well against a white developer. The penetrant is usually sprayed or brushed onto the part, then after the penetrant dwell time has expired, the part is cleaned with a cloth dampened with penetrant cleaner after which the developer is applied. Following the developer dwell time the part is examined to detect any penetrant bleed-out showing through the developer.
Water-washable
Water-washable penetrants have an emulsifier included in the penetrant that allows the penetrant to be removed using a water spray. They are most often applied by dipping the part in a penetrant tank, but the penetrant may be applied to large parts by spraying or brushing. Once the part is fully covered with penetrant, the part is placed on a drain board for the penetrant dwell time, then taken to a rinse station where it is washed with a course water spray to remove the excess penetrant. Once the excess penetrant has been removed, the part may be placed in a warm air dryer or in front of a gentle fan until the water has been removed. The part can then be placed in a dry developer tank and coated with developer, or allowed to sit for the remaining dwell time then inspected.
Post-emulsifiable
Post-emulsifiable penetrants are penetrants that do not have an emulsifier included in its chemical make-up like water-washable penetrants. Post-emulsifiable penetrants are applied in a similar manner, but prior to the water-washing step, emulsifier is applied to the surface for a prescribed period of time (emulsifier dwell) to remove the excess penetrant. When the emulsifier dwell time has elapsed, the part is subjected to the same water wash and developing process used for water-washable penetrants. Emulsifiers can be lipophilic (oil-based) or hydrophilic (water-based).